“With the Development Centre, we are setting the global benchmark in automotive development. Here we are shaping the mobility of today and tomorrow.” Michael Steiner, Member of the Executive Board – Research and Development
Weissach Development Centre – a driver of innovation for 50 years
Porsche celebrated the 50th anniversary of the Weissach Development Centre on 1 October 2021. There are now 6,700 employees developing technologies, components and vehicles at this think tank. The spectrum encompasses everything from design and concept development to model construction and initial prototypes. “With the Development Centre, we are setting the global benchmark in automotive development. Here we are shaping the mobility of today and tomorrow,” says Michael Steiner, Member of the Executive Board responsible for Research and Development at Porsche AG.
The wish for its own test track near to its plant began to grow at Porsche back in the late 1950s. Ferry Porsche performed the groundbreaking for the first construction phase of the new proving ground on 16 October 1961. Various test tracks were initially created on which, among others, the Porsche 911 was taken through to market maturity. Plans for the construction of an integrated research and development centre in Weissach were drawn up in the 1960s. The idea was to pool the expertise that had until then been spread across the sites in Zuffenhausen and Weissach. Construction of the actual Weissach Development Centre began in 1969. Porsche’s Research and Development department and its own Motorsport division then moved to Weissach in 1971. From the outset, the development centre had a workforce of approximately 500.
The Porsche Style department subsequently followed in 1972. The building in the shape of a standard hexagon, which was developed with optimum work and cooperation possibilities in mind and remains characteristic to this day, was then completed in 1974. At the same time, Porsche expanded the development centre’s testing capacities. Further improvements here up to the mid-1980s included a measuring centre for environmental technology and a test building for engines and power units. In May 1986, Porsche opened what was then the most modern wind tunnel in the world.
As automotive engineering advanced, the infrastructural demands made of the development centre changed too. A second approach road, a complete vehicle inspection building, a centre for safety tests and a climatic wind tunnel are currently under construction in the south of the research and development centre. By 2025, the site will have been expanded by 12 hectares. It currently comprises approximately 100 hectares.
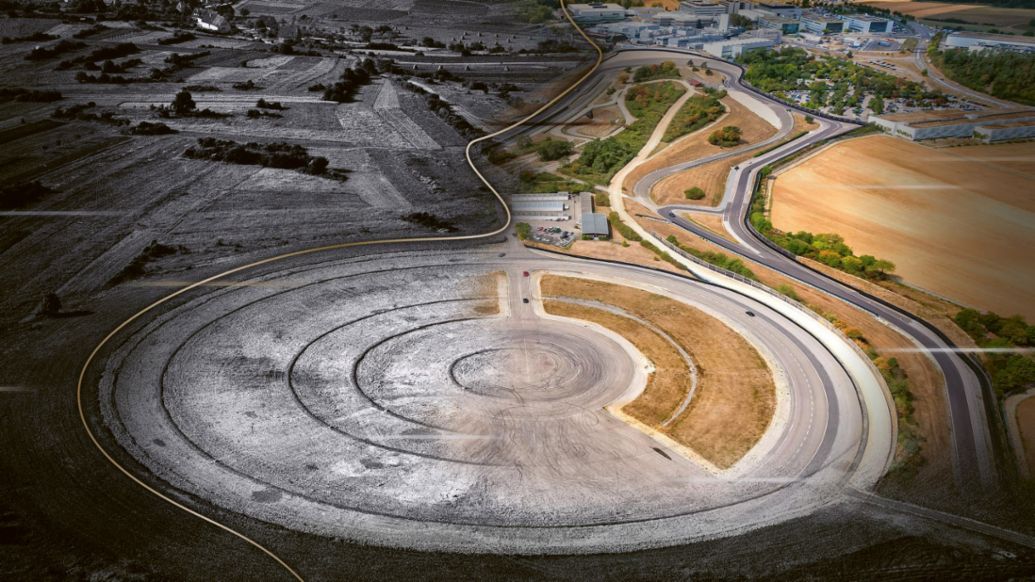
The Innovation Management department founded by the Chairman of the Executive Board of Porsche AG is now key to securing the future of the company.
Turbo for ideas – innovation management at Porsche
“An innovation programme does not invest in patents or inventions. It invests in people.” This maxim uttered by Oliver Blume in 2016 has evolved into a recipe for success. The Innovation Management department founded by the Chairman of the Executive Board of Porsche AG is now key to securing the future of the company. Its task is to assist with Porsche’s transformation into a digital, electrified future and to reconcile the conflict between premium, performance and luxury on the one hand and sustainability on the other.
Ideas with a future are therefore needed. Every idea is more than welcome, no matter where it comes from within the company. Organisational structures have been modified to this end and the prerequisites for cross-functional, cross-departmental work have been created. The employees are afforded the space they need to work creatively. This lays the foundations for innovation. The concept has found fertile soil – 80 to 100 teams or individual employees apply themselves with real dedication every year. Their creative suggestions range from product improvements and production line innovations to innovative digital solutions.
The employees can submit their suggestions either to their own department’s Innovation Manager or via a special IT tool. The Innovation Management department then arranges a time for the employee to present their idea in person and receive immediate feedback. For Porsche to consider an idea an innovation, it has to fulfil three criteria – it has to be new and unique, it has to be profitable for the company and it must offer a relevant customer benefit.
If the feedback given is positive, the project is directly initiated with next to no preliminary work. Active initiative is required in order for the ideas to be further developed. The idea provider also assumes responsibility for project management, but is, of course, given assistance. The Innovation Management department offers assistance with methodology, invests money if applicable and, if needed, contacts potential development partners. These can also be based outside of the company. In this way, the Innovation Management department ensures that innovative project ideas are validated in a structured manner and, in the event of success, can more than likely be further developed through to series production.
To have the shortest possible paths, Porsche AG’s seven departments and Porsche Digital GmbH each appointed one or two employees to Innovation Management. The team pursues a defined innovation agenda to focus its activities on the future topics that are the most relevant to Porsche. The target has been clearly set – the company has earmarked 15 billion euros to be spent on electromobility, digital transformation and sustainable production up to 2025. Of this, more than 800 million euros a year will be spent on digitalisation.
Thinking about innovations is not limited to Porsche as a company. There is a focus in particular on collaboration with start-ups and universities. In some cases, Porsche also invests directly in up-and-coming companies or launches initiatives to expedite digitalisation. More than 150 million euros a year has been earmarked for investment in start-ups and venture capital companies. Porsche Ventures was set up as an ecosystem which can support every start-up, no matter whether there is currently only the idea or whether there have already been some financing rounds. This ecosystem includes the company builder Forward31 and the earliest-stage investor APX, a 50:50 joint venture with Axel Springer, both of which are based in Berlin. With the venture capital unit Porsche Ventures and Porsche Digital GmbH, the company is always on the lookout for new start-ups that will strategically advance the brand.
Porsche’s pioneering spirit extends far beyond its core topic of sports cars. With the initiative for the major eFuels project, the sports car manufacturer triggered the production of synthetic fuels. These have the potential to be almost entirely CO₂-neutral.
eFuels complement e-mobility
Filling up on electricity is possible thanks to eFuels – the go was given in late summer 2021 for the construction of the first factory to be co-initiated by Porsche for the production of a synthetic fuel. This has the potential to be almost entirely CO₂-neutral. The Haru Oni joint project involving Porsche, Siemens Energy and other international partners is the world’s first integrated and commercial plant for the production of synthetic fuels. It makes use of the optimum climatic conditions for wind power found in the southern Chilean Magallanes Province to produce synthetic fuel with the aid of sustainably generated electricity.
Production at the pilot plant in Chile is scheduled to start in mid-2022. In addition to Siemens Energy and Porsche, those involved in the Haru Oni project include the Italian energy company Enel, ExxonMobil and the Chilean energy companies Gasco, ENAP and AME, which is the primary developer and the owner of the project company HIF (Highly Innovative Fuels).
With eFuels, existing vehicles can play their part in a quick CO₂ reduction too. “We urgently need a solution for the sustainable operation of the existing fleets,” emphasises Michael Steiner, Member of the Executive Board responsible for Research and Development at Porsche AG. “This goal can be achieved with green fuels. They are a sensible addition to electromobility.” There are additionally other transport sectors in which these fuels could be used such as aviation and the shipping industry, which are difficult to electrify, if at all.
Low costs for renewable energy are key to quickly making eFuels competitive. The wind turbine at the pilot plant site has a very high capacity factor of 74 per cent full load hours. But in addition to the resultant low energy costs for the production of eFuels in Chile, the price and therefore also the commercial success are determined by taxes and levies. The more the prices of fossil fuels and eFuels are brought into line with one another in the future by means of regulatory measures such as energy taxes or CO₂ pricing, the quicker eFuels will become competitive.
With the methanol-to-gasoline (MTG) process intended for use in the Haru Oni project, the consortium is initially focusing on fuels for petrol engines. Generally speaking, the raw materials water and carbon dioxide are needed to produce eFuels. Hydrogen is produced by means of electrolysis, while carbon dioxide is extracted directly from the air by means of what’s known as direct air capture. Here, huge fans blow ambient air through filters and the carbon dioxide in the atmosphere then accumulates in the filters. Methanol synthesis is used to turn H₂ and CO₂ into e-methanol (CH₃OH), with MTG synthesis then being applied to turn this into synthetic naphtha.
In a subsequent step, the virtually CO₂-neutral fuel is refined such that it complies with the current fuel standard DIN EN 228.
It can then be used directly in any petrol engine or be added to a fossil fuel. In principle, it would take only comparatively minor modifications to the plant for it to be able to also turn e-methanol into, for example, e-kerosene for aircraft.
The pilot plant is expected to produce around 130,000 litres of eFuels a year from 2022. Porsche will buy this entire volume and will initially use the green fuel primarily in its motorsport activities. In addition, Chile has set itself ambitious goals as part of its national strategy for green hydrogen. These include producing the world’s most affordable hydrogen and turning itself into a leading exporter of green hydrogen and its derivatives.
At Porsche Engineering, virtual worlds will be created that replicate all the relevant road situations, serving as test cases for the driver assistance systems’ algorithms and sensors. Game engines from the computer games industry are used for this.
Digital validation of driving functions
Sporty performance and automated driving in one and the same car – approximately one in four Porsche customers in the key Porsche markets around the world is considering buying a vehicle which can itself take on the responsibility of driving in certain situations. The sports car manufacturer is therefore working intensively on concepts and technologies that will enable automated driving functions.
However, the sensor technology and data processing requirements are so complex that they far exceed the capabilities of conventional development and proving methods with physical test cycles.
Many test kilometres are therefore moved to the laboratory in the form of digitalisation and extensive computer simulations. The engineering services are provided by Porsche Engineering, a wholly owned subsidiary of Porsche AG. It has begun with the development of the Porsche Engineering Virtual ADAS Testing Center (PEVATeC) for this purpose. ADAS stands for “advanced driver assistance systems”. In this laboratory, virtual worlds will be created that replicate all the relevant road situations, serving as test cases for the driver assistance systems’ algorithms and sensors.
Not only are the test drives in a simulated environment less expensive, save time and involve less organisational work. It is also possible to simulate and adapt critical situations from real road traffic during the virtual test drives, based on the needs.
In addition to the real-time capability of the simulations, an aspect which is at least as important is that the virtual worlds generated by the computer produce physically realistic effects. Digitally replicated objects such as roads, pavements, building walls and vehicles have to have precisely the same properties as can be found in real road traffic – only then can they provide the camera, lidar, radar and ultrasound systems with realistic input.
Porsche Engineering uses game engines from the computer games industry for this. These frameworks generate photorealistic images and ensure that the physical behaviour of objects in computer and video games is correct. Porsche Engineering develops and tests virtually automated driving functions with the aid of these software packages. Together with artificial intelligence, game engines have a key role to play, training the driver assistance systems with synthetic sensor data. This allows any scenario and every eventuality to be gone through in detail.
Drives simulated with the aid of game engines have the advantage of it being possible to repeat them again and again, of being controllable and of taking less time. They are additionally used in vehicle construction in order to reduce the number of actual prototypes and thus save time and money. For this, Porsche Engineering uses its internally developed Visual Engineering Tool, which allows, for example, questions regarding the optimum arrangement of parts to be answered quickly and inexpensively on the basis of CAD data and augmented reality (AR) or virtual reality (VR) glasses.

Porsche analysed priorities and use cases to identify the optimum battery size. Porsche customers set great store by driving dynamics. At the same time, they expect short journey times and quick recharging when making long-distance journeys.
Commercially available high-voltage battery repairs
Porsche thinks ahead – the sports car manufacturer has pursued a holistic approach in the area of electric vehicles with high-voltage batteries since the first generation of hybrid models was rolled out in 2013. This approach covers everything – procurement, manufacturing, advisory services, sales, logistics and recycling.
The repair concept for high-voltage batteries likewise makes a significant contribution to sustainability and the conservation of resources. When developing batteries, Porsche pays attention from the outset not only to efficient manufacturing possibilities, but also to a set-up which is so simple that the battery can subsequently be repaired at qualified Porsche Centres. Either 28 or 33 modules are installed depending on the Taycan derivative’s battery capacity. The battery housing can be opened and the cell modules and other components can be replaced. A custom repair level therefore also offers the customer a cost advantage.
Cell modules that still work but which are no longer suitable for use in the vehicle can be used for stationary tasks. As part of its second-life strategy, Porsche is working on a pilot project that will allow high-voltage batteries to be reused. They are dismantled down to the module level and installed in stationary energy carriers. A series solution is key when it comes to the long-term, sustainable reuse of old batteries.
Together with the Volkswagen Group and other expert partners, Porsche continues to optimise the existing recycling processes with the aim of increasing the proportion of raw materials in circulation and then using these in new batteries.
A comprehensive concept has also been put in place for the servicing of Porsche’s all-electric model as the servicing and repair requirements of the Taycan are very different to those of a vehicle with an internal combustion engine. The repair work performed on electric vehicles calls for specific expertise and special tools that the Porsche Centres need to be newly equipped with. The service concept for electric vehicles therefore comprises multiple levels. The basic level is the high-voltage base set up at a qualified Porsche Centre. Where there is currently no high-voltage base in the vicinity, the sports car manufacturer sets up transregional hubs for high-voltage vehicle repairs.
If transportation to a suitable repair location isn’t possible, a “flying doctor” steps in. This is a mobile high-voltage expert who repairs faulty high-voltage batteries on-site. This completes the seamless service network for high-voltage battery repairs.
Last, but not least, a clear breakdown of the tasks and responsibilities is also necessary when working on the Taycan as the first production vehicle with system voltage of 800 volts. Porsche has defined three qualification levels here – persons trained in electrical engineering, high-voltage technicians and high-voltage experts. Persons trained in electrical engineering have a basic qualification to perform standard repairs. High-voltage technicians have training in activating a vehicle’s voltage and in categorising and storing lithium batteries. Their qualification also includes the disassembly and packing of high-voltage batteries with a “normal” and “warning” status. High-voltage experts have the highest level of qualification at a Porsche Centre. Only they are authorised to perform work within high-voltage batteries, handle high-voltage batteries with insulation defects and prepare and pack such batteries for transportation.
Battery development between range, performance and sustainability
The goal has been clearly defined – Porsche is aiming to be balance-sheet CO₂-neutral all along the value chain by 2030. The schedule for the company’s Production and Logistics departments has been systematically aligned with this. The key role will be played by the progress made with electromobility.
These days, close to half of all the CO₂ emissions generated in the course of an electric vehicle’s life cycle are caused during its manufacture. This includes raw material extraction and processing. The second biggest factor is the car’s operation, which depends on the energy mix, its charging and vehicle efficiency and the driving style. Recycling at the end of the vehicle’s life cycle accounts for the smallest share of CO₂ emissions.
Of the individual factors, it is above all the traction battery which has a major influence on CO₂ emissions during the life cycle – around 40 per cent of the carbon dioxide generated during the manufacture of a single Taycan can be attributed to the battery. In other words, the battery size is largely responsible for an electric vehicle’s emissions balance. It also influences the market success as the dimensions have to meet the customers’ requirements and expectations.
The best results are achieved with a mediumsized battery where the optimum driving dynamics balance has been struck between weight and efficiency.
Future developments will further improve the driving dynamics and reduce the charging time. Even greater progress can be expected with regard to reducing CO₂ emissions. The second generation of electric vehicles, which will be rolled out shortly, will release around a quarter fewer carbon dioxide emissions over its life cycle than the first generation. Above all, however, battery technology will significantly improve the environmental footprint – new cell technologies will lower energy consumption, while better charging capacity will improve efficiency. The proportion of recycled raw materials from batteries is set to grow. This is helping the target set of balance-sheet CO₂ neutrality throughout the value chain by 2030 to be achieved.
Moving into the manufacture of high-performance battery cells
Porsche is actively moving into the manufacture of high-performance battery cells through its investment in the Cellforce Group. The Cellforce Group is a joint venture between Porsche and Customcells GmbH. A planned production facility is scheduled to have an initial capacity of at least 100 MWh a year from the end of 2024. This equates to high-performance battery cells for some 1,000 vehicles. The cells are special lithiumion battery cells for use in motorsport and in high-performance vehicles. The chemistry behind the new high-performance cells revolves around silicon as the anode material. This makes it possible to considerably increase the energy density compared with the current production batteries. The battery can be more compact in design while offering the same energy content. This new chemistry also reduces the battery’s internal resistance, enabling it to absorb more energy during energy recuperation and making it more efficient during fast charging.

A “digital twin” is the virtual copy of a physical vehicle and it allows for data-driven analysis, monitoring and diagnos- tics – minus the real-world costs and constraints.
Digital chassis twin for predictive driving functions and component statuses
The performance of the integrated sensor technology, connectivity and data processing improves with every new Porsche generation. New opportunities to use all this information effectively therefore present themselves all the time. One of these is what’s known as a digital twin. This is the virtual copy of a physical counterpart and it allows for data-driven analysis, monitoring and diagnostics.
A vehicle’s digital twin consists not only of the operating data collated, but also of its consequences – information which is gathered during scheduled servicing and unplanned repairs. Parts of this digital twin therefore already exist in the memory of control units and in the Porsche Centre databases.
The huge potential of the digital twin lies in the fact that its data is pooled in a centralised intelligence system. Conclusions that benefit every single vehicle and therefore every individual customer can be drawn from data relevant to an entire field. With this big data, an algorithm can then calculate the driving style on the basis of, for example, sensor data from the engine and chassis and recommend not only the vehicle’s optimum service time, but also the servicing scope. And more importantly, component wear and even potential failures can be calculated in the same way even before they actually occur – resulting in a considerable safety bonus.
For around three years, Porsche’s software specialists have been working on the concept of a digital twin with a focus on the chassis, that is to say a “chassis twin”. This project is now being continued by CARIAD, the Volkswagen Group’s independent automotive software company. The advantage of this is that, rather than only Porsche vehicle data being drawn on, data can be sourced from all the Group brands, thus increasing the pool of vehicles by a factor of up to 20.
With a Porsche, it is the chassis that is subjected to the greatest loads, in particular when racing on circuits. The development of a digital twin therefore starts with the chassis. Forces are identified in the vehicle immediately and are communicated to the driver thanks to sensor technology in the vehicle and the intelligent, self-learning algorithms used for centralised analysis. This increases passenger safety because certain malfunctions are flagged up immediately before the vehicle user or the repair shop identifies the error on the basis of, for example, noises or vibrations.

The digital twin offers customers advantages above and beyond vehicle operation too. The digital vehicle file can show the vehicle’s residual value, thereby increasing trans-parency for the buyers and sellers of used cars.
Porsche is already putting the digital chassis to the test in practice. The component being monitored is the air suspension in the Porsche Taycan. In the pilot project, body acceleration data is initially primarily being used to calculated thresholds. If these thresholds are exceeded, the PCM system prompts the customer to have their chassis checked at a Porsche Centre. In this way, it is ensured that the wear limit is not exceeded and consequential damage is prevented thanks to repairs being performed promptly. Both at the testing and production stage, data protection takes top priority. The customers’ consent to anonymised data being transferred is therefore sought via the PCM system. Approximately one in two Taycan customers is participating in this pilot project, representing very positive feedback for this use of the digital chassis.
The digital twin offers customers advantages above and beyond vehicle operation too. The digital vehicle file can show the vehicle’s residual value, thereby increasing transparency for the buyers and sellers of used cars. In addition, there could conceivably be an extended approved manufacturer’s warranty based on seamless documentation of components or even certification with a price recommendation for reselling a vehicle.